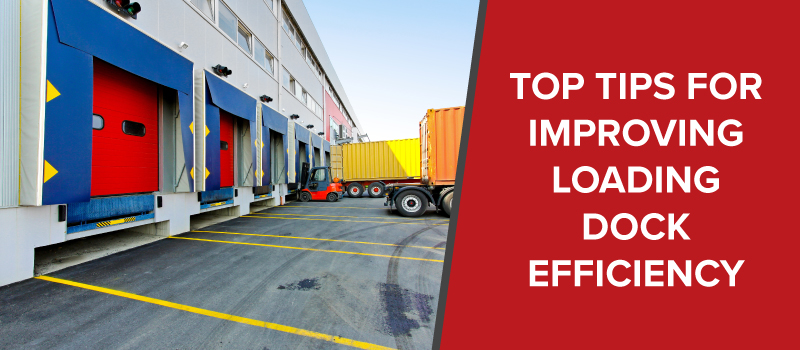
All distribution centers have one thing in common – the material handling zone (MHZ), or what’s commonly called the loading dock. The loading and unloading portals are the connecting point between the yard and the warehouse in all manufacturing or distribution facilities. The docks are where goods are shipped or received depending on incoming or outgoing trucks. They’re the conduit between business operations and the outside world.
Virtually every manufacturing and warehousing facility imports or exports products. That might be finished goods destined for the retail market, perishables going to food stores or raw materials that are used in a manufacturing process. No matter what the commodity, all of these shipments are going to pass through the dock area. Docking takes time, and time is money. That’s why efficiency in the loading dock area is important for maximizing a business’s bottom line.
Contact us online
Give us a call at 877-350-2729
Jump To Sections:
- Loading Dock Efficiency Impacts Your Bottom Line
- Loading Dock Efficiency Tips
- Start With Your Dock Design
- Invest in Excellent Material Handling Equipment
- Automate Your Loading Dock
- Improve Your Loading Dock Communications
- Create a Healthy Loading Dock Environment
- Maintain a Safe and Efficient Loading Dock
- Organize Your Time Efficiently
- Invest in Loading Dock Efficiency Solutions
Loading Dock Efficiency Impacts Your Bottom Line
The loading dock or material handling zone is a critical component in warehouse productivity that includes shipping, receiving and staging areas. There are many factors that affect efficiency. They include dock design and positioning, trailer sizes and shapes, load configurations, and equipment systems used in the MHZ. It’s the place where product shipments interact with material handling vehicles and other equipment. Docks are busy places, and they can be hazardous environments, especially when they’re not designed, equipped and managed efficiently.

Efficient and smooth-flowing material handling zones allow companies to avoid costly delays, prevent spoilage or damage to goods and meet tight schedules by revolving traffic quickly. An ideal MHZ that runs at peak efficiency is properly designed, equipped and maintained. Increasing loading dock efficiency and reducing logistics costs should be a top priority for a facility manager. With effective loading dock procedures and processes, there are significant productivity gains as well as energy savings and reduction in accidents involving equipment and employees. All this affects your bottom line.
Loading Dock Efficiency Tips
Efficiency is all about getting the job done as quickly as possible while generating the lowest cost. That includes unnecessary waits while trucks sit idling and needless trips while workers shuffle material about. Improving efficiency takes many paths, but they all end at the same destination — a profitable company that meets or better yet exceeds customer expectations and surrounds workers in a safe and productive environment.
Getting the most out of time on the loading dock happens through company leadership. Astute managers are constantly looking for ways to improve business processes. Some improvements are minor, and some require major overhauls of company infrastructure and corporate culture. But for the most part, efficiency improvements are made one step at a time, just like these tips are laid out.
Tip #1 — Start With Your Dock Design
Poor loading dock design is probably the number one reason for inefficiency in the material handling zone. Sometimes this is due to purchasing a building that was occupied by a tenant in a different business line. The dock area may have been designed with a different flow pattern or had lesser traffic flow.
“Bottleneck”, for example, is the common term for poorly designed loading docks that get inundated with more shipping and receiving activity than they can handle. This leads to a domino effect which affects the efficiency of truckers who need to get back on the road to finish their routes and the success of facility workers who have to deal with jammed dock platforms and plugged aisles.
Bottlenecks are usually due to insufficient space. They can be overcome by properly designing accessories that make the space more operational. Larger overhead doors and better dock leveling height can help to ease the flow. Loading dock doors should be a minimum of 10 feet by 10 feet to accommodate today’s large semi-trailers. Vertical stacking is another way to increase the use of limited dock space.

The time to start dock design is before the structure is built. Loading docks are such a vital component in a manufacturing and warehouse facility that they need the professional attention right from the early planning stage. Dock design should be a team approach with everyone’s input. That includes the most important team members —the workers who do day-to-day material handling tasks and work on the loading dock.
Good loading dock designs also take into account how every piece of material handling equipment works in efficient harmony with one another. Pay attention to how each of your material handling tools interfaces on the loading dock. Consider all these important tools that you find on loading docks and incorporate their best use into your dock design:
- Pallet trucks: Also called pallet jacks, these vital tools can be powered by manual strength or electric motors. Check out the huge selection of pallet trucks that Cherry’s Industrial Equipment stocks.
- Industrial hand carts: These are especially useful for quickly moving lighter loads from the warehouse, out to the dock and onto waiting trailers. Make your dock more efficient by choosing from drum carts, hardwood platform carts and even collapsible industrial carts.
- Heavy transport dollies: Dollies are workhorses that efficiently handle heavy loads like machines on skids and loaded tanks. Choose from individual, tandem and steerable transport dollies.
- Pallet stackers: You get a lot of dock efficiency with pallet stackers. Cherry’s Industrial handles a variety of manual, semi-electric and full-powered pallet stackers.
Material handling suppliers like Cherry’s Industrial Equipment should also be involved in loading dock design. Representatives that supply pallet trucks, industrial hand carts, pallet stackers and heavy transport dollies are intimately familiar with every material handling piece. Make sure you consult with a Cherry’s Industrial rep who can help make your loading dock more efficient.
Contact us online Give us a call at 877-350-2729
Tip #2 — Invest in Excellent Material Handling Equipment
Great material handling managers plan the right loading dock design, create safe and healthy environments and improve workplace communications. They also know the value in purchasing excellent equipment to help make the loading dock highly efficient.
Some of the efficient equipment purchases are large investments like automated, data-based management systems or even a total overhaul of the loading dock area by incorporating it with smooth flowing conveyors, wrappers and powerful lifts. Not all efficient equipment needs to be fancy or expensive. Simple safety devices can make a serious impact on efficiency, and these are often easy to implement.

Cherry’s Industrial Equipment is a top supplier to America’s material handling industry and has excellent equipment in place all across the nation’s loading docks, making them safer and highly efficient workplaces. We supply stock items as well as partner with distribution centers to custom design and build specific equipment to work with leading loading dock designs. We also handle efficient equipment that improves loading dock processes. Some of the most popular items are:
- Stretch wrapping machines: These efficient, labor-saving devices are available as turntable wrappers, overhead mast wrappers and automatic wrapping machines that work in conjunction with conveyors and automated assembly lines.
- Industrial pallets: Choose from a host of industrial pallets including stackable, rackable and nestable pallets. We have plastic, aluminum and wire mesh pallets to help organize your dock efficiency.
- Roller skids, machine skates, hydraulic toe jacks and transport dollies: These labor-saving devices allow heavy materials to be quickly and conveniently moved onto the loading dock and into waiting trailers.
- Industrial carts: Every loading dock needs industrial carts to efficiently and safely move materials on the dock floor and into the trailer. Cherry’s Industrial carries an extensive stock of carts including collapsible models as well as power propelled.
- Pallet trucks: Pallet jacks are a staple material handling tool on all loading docks. They’re available in light-duty pallet truck models that are manually operated right up to heavy-duty pallet jacks that are electrically powered and controlled by an operator.
- Pallet stackers: These machines are indispensable for your warehouse and loading dock. Pallet stackers take the heavy lifting away from your workers and let them efficiently place and retrieve stacked pallets.
Tip #3 — Automate Your Loading Dock

Automating your loading dock processes can greatly increase your performance by cutting down on manual planning and data recording hours for your employees. There are a variety of ways you can implement loading dock automation for your business, including:
- Stretch wrapping machines: These automated machines are irreplaceable when it comes to organizing your loading dock. Stretch wrapping loaded pallets provides safety and security to your shipments. Hand-wrapping stretch film is laborious and inefficient. Investing in a stretch wrapping machine from Cherry’s Industrial Equipment may be the best organizational move you can make. Choose from turntable, overhead-arm or automated robotic stretch wrappers.
- Global Positioning Satellite (GPS) and Radio Frequency Identification (RFID) technology: These components let the loading dock controller be aware of exactly which trailers are present, which have left and which are inbound, as well as knowing exactly which goods are attributed to the assigned load. This saves an enormous amount of human time and greatly reduces the chance of costly errors.
- Warehouse Management Systems (WMS): Some managers spend a lot of funds and effort on automating their warehouse inventory accounting and tracking systems. But they fail to integrate the shipping and receiving areas with their WMS. The lack of total integration creates a left-hand/right-hand conflict or lack of communication — and a sure spot for inefficiency.
- Automated equipment: You can incorporate automation into overhead doors, leveling ramps, vehicle restraint systems, coordinated light signals and sensors that detect trailer movement. Teleconveyors are especially effective in automating the transfer of goods from warehouse shelves to trailer beds. Teleconveyors remove the time-consuming steps of forklift or human travel, but this automated system is rarely used.
- Efficient dock layouts: The impact of an inefficient dock layout expands from the dock center out to the yard and into the warehouse. Distances between event stations are too far removed, causing excessive trips and a waste of worker time. Inefficiency in layout also causes excessive wear on machinery and unnecessary energy consumption. This can be rectified by paying attention to detail and improving loading dock design.
Contact us online Give us a call at 877-350-2729
Tip #4 — Improve Your Loading Dock Communications
One of the biggest slips in efficiency at all workplaces happens from poor communication. Good communication goes beyond verbal exchanges or digital documentation. It involves an entire system where everyone in the facility knows what they’re doing and how it affects fellow workers and the company as an entity. Good communication happens right from instructing workers on the overall loading dock operation all the way down to specifics like how to secure a pallet.

There are many communication forms at work on a loading dock, which all play a key part in ensuring operations run smoothly, efficiently and safely. Be sure to have a mindful process in place for the following types of communications:
- Verbal communication: Spoken communication between workers can be compromised by the noise factor on loading docks. Trucks, forklifts and the hum from rollers and machinery can overwhelm workers and cause them to miscommunicate. Investing in personal communication devices like earpiece inserts and handheld visual displays will improve signals and reduce confusion.
- Advanced communication light systems: Exterior color-coded lights instruct truck drivers which docks to align with as well as when it’s safe to proceed. Interior traffic lights let workers know when it’s safe to cross forklift paths and when to remain out of the way. Indicator lights mounted at the top corners of dock doors let managers know what stage of loading a particular trailer is at. This simple but efficient system lets them keep traffic flowing.
- Wireless communication technology: Stock Keeping Unit (SKU) information can immediately be relayed to a central processing center by a quick swipe of a bar code scanner. GPS and RFID tracking let the center know automatically where inventory, trailers and machinery are located and what stage of shipping they’re at.
- Online order processing: Digital order processing greatly reduces the amount of paperwork that goes along with waybills and inventory receipts. Far fewer mistakes are made when there is isn’t any written documentation to get lost, wet or sent with the wrong load. All of this digital technology is part of an automated warehouse management system that needs to include the loading dock as part of the overall plan.
- Efficient appointment booking: Appointments are the times allotted for a trailer to arrive and depart at a terminal’s dock, and these are often made days or weeks in advance. It’s a critical component in efficiently moving goods about the nation. Using the best of current technology to make sure shipping appointments are set and met greatly helps the efficiency of a material handling zone.
Tip #5 — Create a Healthy Loading Dock Environment
Many of the health hazards in a loading dock environment can be eliminated or minimized by attention to detail in planning and incorporating solutions in the overall design. A healthy loading dock is going to be a much more efficient workplace. It’s also going to be more productive and cost effective.
Be sure to pay close attention to the following health concerns when designing your loading dock:
- Ventilation: These material handling areas have both indoor and outdoor environments that are often exposed to each other. Most large trucks are diesel powered, and their exhaust fumes can be overwhelming, especially at cold times of the year. Investing in fans or mechanical ventilators greatly contributes to an efficient loading dock environment.
- Temperature: Worker comfort has an enormous impact on efficiency and productivity. Workplaces that are extremely hot or cold can be so uncomfortable that they’re almost unworkable. Products are also weather and temperature sensitive. Perishables need to be protected from cold. Heat is another threat that can destroy certain products like electronics and pharmaceuticals. An effective climate control system plays a big part in making loading docks efficient.
- Lighting: OSHA regulations set out health and safety requirements for loading dock illumination, but they’re the minimum standards. Good managers understand that their workers need full visibility to handle material efficiently. There should be ample lighting everywhere on the dock and also auxiliary lighting that can be carried into the trailer. Trailers usually have limited interior lights, and this can easily be brightened with loading dock extension lamps.
Contact us online Give us a call at 877-350-2729
Tip #6 — Maintain a Safe and Efficient Loading Dock
Worker safety is another huge concern when considering how to improve loading dock efficiency. Every effort at boosting loading dock efficiency should make safety practices a top priority. Docks are a hub of activity and full of heavy materials and moving equipment. Poorly designed and badly outfitted loading docks present a greater safety risk to workers than docks that are given proper care and attention.

Many efficient improvements walk hand-in-hand with safety controls and devices. Safety is difficult to put a true price on, but a working safety program can be priceless. The best-performing companies have safety as a core corporate culture. It’s the way they do business, and that includes the performance at their loading docks. Consider incorporating these safety features into your corporate culture. You can source them through Cherry’s Industrial Equipment:
- Safety guards and barriers: Every loading dock needs to be equipped with safety devices to guide traffic safely about the MHZ. Cherry’s Inudstrial guards and barriers are highly visible and exceptionally efficient.
- Bollards and column guards: Safety devices protect people as well as trucks, trailers and buildings from accidental collision. Untold savings are gained from a small investment in Cherry’s Industrial columns and bollards.
- Safety signs and visual aids: Factory and warehouse applications need visual signals. These include warnings for hazards and floor safety. Custom signs can also be supplied.
- Safety marking for aisles, floors and dock edges: No loading dock can have efficiency in the safety department without having hazards clearly marked. This includes tripping and spacing hazards as well as identifying aisles for safe and efficient travel.
- Storage cabinets: Another big safety issue to address when organizing your loading dock is storage. Cherry’s Industrial carries an excellent selection of specialized storage cabinets for corrosive, flammables and environmental protection as well as housing gas cylinders, ink and paint.
- Pallet truck stops: No loading dock should be organized without having pallet truck stops in place. These inexpensive devices prevent pallet trucks from rolling when unattended.

Cherry’s Industrial Equipment carries a full line of warehouse and loading dock safety supplies. That includes storage containers, signs, barriers and stops. We can also fulfill custom orders. Contact a representative to discuss your custom needs.
Tip#7 — Organize Your Time Efficiently
Organizing for loading dock efficiency takes workers’ time into account. There is a lot of wasted time and energy occurring in loading docks across the nation. There are also changing rules that govern the trucking industry, and they directly affect stationary facilities.
Recently, the Federal Motor Carrier Safety Administration (FMCSA) adjusted maximum daily hours for long-distance drivers so that stationary time is included in their allowable shifts. That means an extra hour or two at the loading dock cuts into their billable driving time. This makes efficiency even more important going forward as trucking time has to be accomplished quickly.
Another main reason for inefficiency is not applying current technology and automation in the material handling zone. There are tremendous tech tools available to reduce packaging, loading and shipping time that, in turn, lower labor and material costs. They also lower workplace injuries, which are expensive for downtime and can increase insurance rates.

Converting to automation can be a large capital investment, but it quickly pays back in improved efficiency and revenue streams. Conversion doesn’t have to be done at one time — rather, it can be implemented a step at a time. It’s all about finding efficient solutions.
Tip #8 — Invest in Loading Dock Efficiency Solutions
All efforts at improving loading dock efficiency should focus on reducing the time and labor involved in getting shipments processed. The faster a shipment happens, the greater the return on revenue and customer relations. Excellent load sequencing takes concentrated effort and strategic planning. Efficient material handling is a core company competency and a mark of professionalism.
The best efficiency you can get on your loading dock is to integrate all the material handling and safety products that Cherry’s Industrial Equipment provides. Efficiency comes with combining the features and benefits of all sorts of tools and protective devices. Consider your overall efficiency picture when you invest in all of these loading dock efficiency tools:
- Stretch wrapping machines
- Pallet trucks or pallet jacks
- Roller kids
- Machine skates
- Industrial carts
- Plastic and metal pallets
- Hydraulic toe jacks
- Transport dollies
Cherry’s Industrial Equipment strives to make workplaces like loading docks safe, secure and efficient. We work with you to find solutions for loading dock efficiency as well as equip you with the best quality and value in industrial investments.

Talk to a Cherry’s Material Handling representative today to discuss solutions for improving your loading dock efficiency.